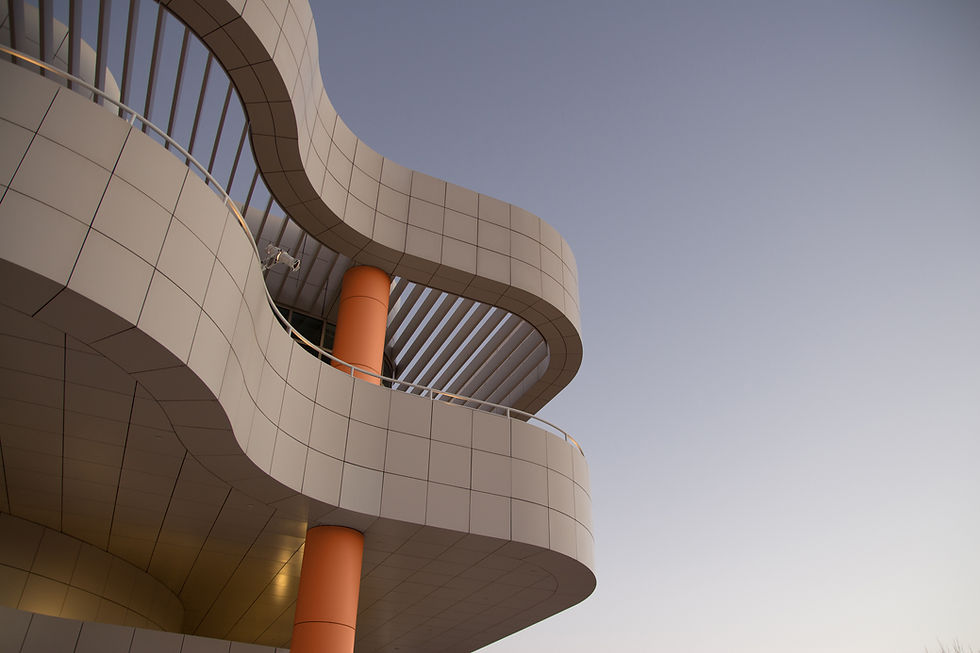
Understanding Calibration and Testing of Personal Gas Detectors
Oct 4, 2024
5 min read
0
2
0

Personal gas detectors play a crucial role in ensuring the safety of workers in hazardous environments by providing real-time alerts of dangerous gas concentrations. However, like any sophisticated equipment, they require regular maintenance to remain effective. One of the most important aspects of this maintenance is calibration and testing. Understanding how to calibrate and test these detectors properly ensures they function accurately and reliably, ultimately protecting workers from potentially life-threatening situations.
What Is Calibration?
Calibration is adjusting the gas detector's sensor to ensure it accurately measures gas concentrations in the air. Over time, the sensitivity of gas sensors can degrade due to environmental factors such as exposure to high gas concentrations, dust, humidity, or extreme temperatures. Regular calibration compensates for these changes, ensuring the detector provides accurate readings.
Calibration involves comparing the gas detector's readings with a known concentration of a test gas, typically called a "calibration gas." If the detector's reading deviates from the known concentration, adjustments are made to align it with the actual values.
Why Calibration Is Important
Accuracy of Readings: Gas detectors are only as reliable as their ability to detect gas concentrations accurately. If the sensor has drifted over time without recalibration, it could lead to false alarms or, more dangerously, fail to detect harmful gases when they are present. Regular calibration ensures that the detector remains sensitive to even small changes in gas concentration.
Regulatory Compliance: Many industries, including oil and gas, chemical manufacturing, and construction, are governed by strict safety regulations. These regulations often require that gas detectors be regularly calibrated and tested to maintain compliance. Failure to do so could result in penalties or serious workplace accidents.
Preventing False Alarms: Over time, sensor drift can cause detectors to trigger false alarms, which may lead to unnecessary evacuations or work stoppages. Regular calibration helps prevent such incidents, ensuring the detector only alarms when actual danger is present.
Types of Calibration
There are two main types of calibration: zero calibration and span calibration.
Zero Calibration: Zero calibration sets the detector's baseline reading. This is done by exposing the detector to a gas-free environment (or air without the target gases) to ensure the reading is zero. This process is essential to confirm that no background gas affects the readings.
Span Calibration: Span calibration involves exposing the detector to a known target gas concentration. For example, if you are calibrating for carbon monoxide (CO), the detector would be exposed to a test gas containing a precise concentration of CO, such as 50 ppm (parts per million). The detector is then adjusted to reflect the accurate concentration, ensuring that future readings will be correct.
Calibration Frequency
The calibration frequency depends on several factors, including the manufacturer's recommendations, the environment in which the detector is used, and regulatory requirements. Most manufacturers recommend calibrating gas detectors every 6 to 12 months. However, more frequent calibration may be necessary in high-risk environments where gas exposure is frequent.
For example, gas detectors used in confined spaces or areas with high gas concentrations may require monthly calibration to ensure accuracy. Additionally, recalibration should be conducted immediately if a detector has been exposed to high gas concentrations or has undergone significant environmental changes.
Bump Testing
In addition to regular calibration, bump testing is an important procedure ensuring gas detectors function correctly. A bump test is a quick, daily, or pre-use test in which the detector is exposed to a small amount of test gas to verify that the sensors, alarms, and other critical components are working properly.
Bump testing is not a substitute for calibration, but it serves as a functional check to confirm that the gas detector is responsive and capable of detecting gases. Unlike calibration, which involves adjusting the detector to match a known gas concentration, a bump test verifies that the detector can detect gas and trigger an alarm.
How to Perform a Bump Test
Prepare the Test Gas: Obtain a small, portable test gas canister containing the target gases in known concentrations. Ensure that the test gas corresponds to the types of gases the detector monitors.
Expose the Detector: Place the gas detector in a controlled environment and expose it to the test gas for a short period (typically a few seconds). The detector should register the presence of gas and activate its alarms (audible, visual, or vibrational).
Check the Alarms: Ensure the detector's alarms activate appropriately when exposed to the test gas. The detector may require recalibration or sensor replacement if the alarm fails to trigger.
Record the Results: Record the bump test results, noting any issues or malfunctions. If the detector passes the bump test, it is safe to use in the field. If not, further investigation or maintenance may be required.
Key Differences Between Calibration and Bump Testing
Calibration adjusts the sensor to ensure accurate gas concentration readings, while bump testing verifies the detector's basic functionality, ensuring it responds to gases.
Calibration is typically performed less frequently (every 6–12 months), while bump tests are often conducted daily or before each use.
Calibration requires specialized equipment and adjustment of the detector's settings, whereas bump testing is a quick check that involves minimal intervention.
Common Calibration and Testing Challenges
Sensor Drift: Over time, gas detector sensors can experience "drift," where their readings become less accurate due to environmental exposure. Regular calibration compensates for this drift, but it can lead to faulty readings or missed gas leaks if left unchecked.
Calibration Gas Shelf Life: Calibration gases have a limited shelf life, meaning their concentration can change over time. Using expired calibration gas can result in inaccurate calibration, so it's important to ensure that the test gases are fresh and properly stored.
Environmental Factors: High humidity, dust, and extreme temperatures can affect gas detector performance. These factors must be considered when calibrating and testing detectors, as they may influence sensor sensitivity.
Human Error: Incorrect calibration techniques, such as using the wrong concentration of test gas or failing to follow manufacturer instructions, can result in inaccurate calibration. Proper training is crucial to ensure that calibration and testing are performed correctly.
Conclusion
Understanding the calibration and testing of personal gas detectors is vital to ensuring their reliability and effectiveness in safeguarding workers from hazardous gases. Regular calibration keeps detectors functioning accurately, while bump testing ensures they remain responsive in everyday use. By committing to a rigorous calibration and testing schedule, employers and safety officers can protect their workforce from potentially life-threatening gas exposure, ensure compliance with safety regulations, and foster a culture of safety in high-risk environments. In Singapore, where strict safety regulations govern many industries, proper calibration and testing of personal gas detectors are essential for maintaining occupational safety standards. Through careful attention to these procedures, companies can continue to rely on their gas detection equipment to prevent accidents, protect workers, and promote a safe working environment.